Company
Mould your ideas into perfection.
Schmiedeberger Gießerei GmbH not only produces high-quality castings, but is also a reliable partner who understands your needs and fulfils your requirements. Thanks to our many years of experience and state-of-the-art technologies, we can offer you customised solutions from conception to series production.
Benefit from our flexibility, which enables us to efficiently realise both individual projects and large production quantities. We are not only available to you as a manufacturer, but also as a consultant who supports you in selecting the right materials, designing your castings and many other steps.
With the best expertise at your side.
With us as your partner, you can be sure that you will be able to utilise the full potential of casting technology and thus develop your products in the best possible way.
We are ready to invest our expertise and commitment in your projects and look forward to working with you.

Mission statement
Our values guarantee your success, because they serve as a guideline for all our actions.
Mission statement
Social commitment
In our foundry, we place a strong focus on sustainability and social commitment, because we firmly believe that responsibility for the environment and the community are inextricably linked.
Social commitment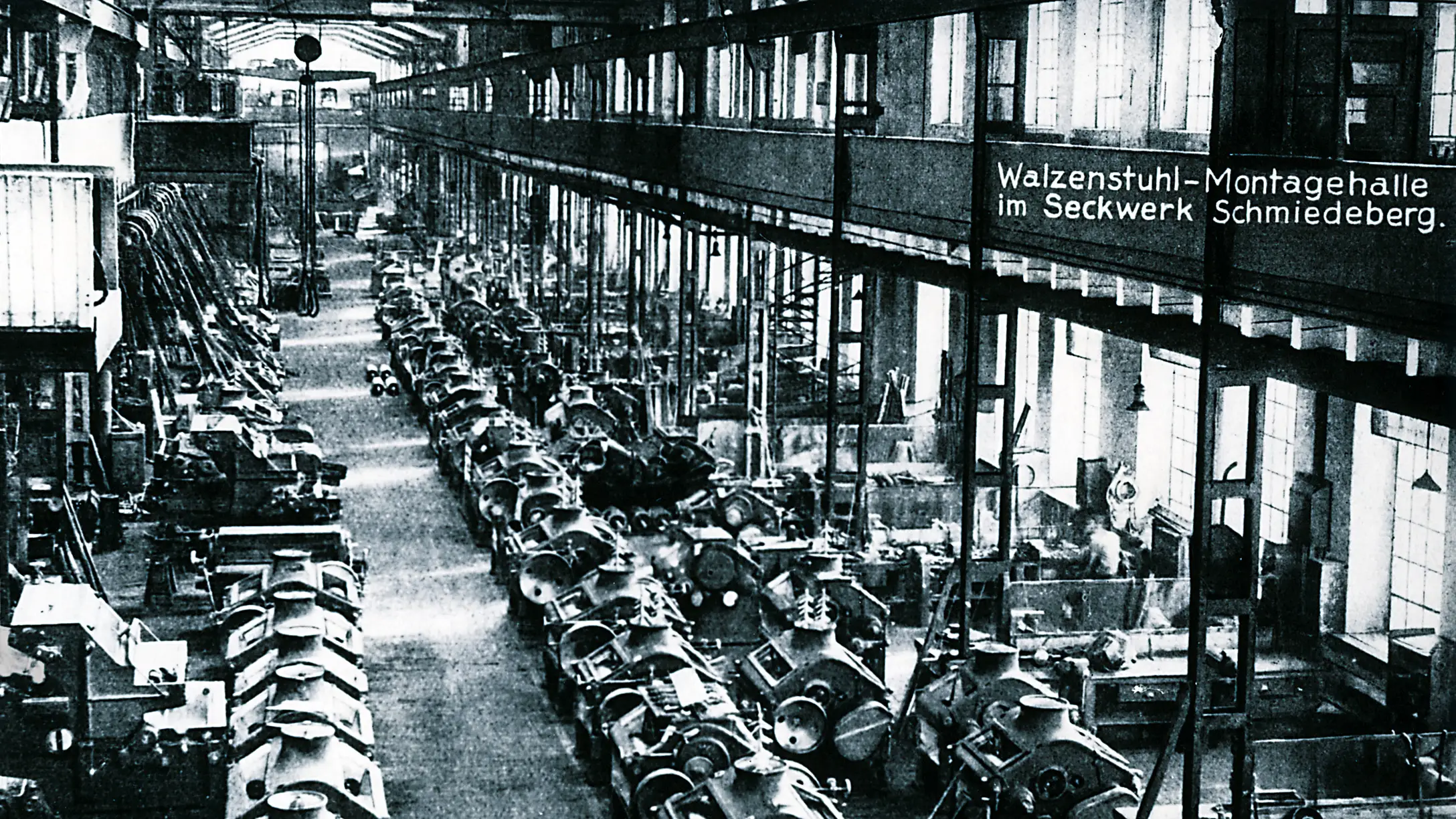
History
Schmiedeberger Gießerei GmbH is one of the oldest subsidiaries of the DiHAG Group. Discover the different phases of the company's development since 1412.
HistoryIndustry expertise
We supply the industries:
-
Mechanical and electrical engineering
-
Vehicle construction / agricultural & construction machinery / rail vehicles
-
Wind power
-
Pumps and fittings
-
Mould construction
-
Customer moulding
Customers & Partners
with whom we work successfully:
Equipment
Our modern production facilities ensure reliable and effective production of your orders.
Moulding plants
Moulding plant 1
Mould sizes
-
Top box 900 x 700 x 250 mm
-
Lower box 900 x 700 x 200 mm
Moulding plant 2
Mould sizes
-
Top box 1400 x 900 x 400 mm
-
Lower box 1400 x 900 x 400 mm
Moulding sand preparation
-
Automatic preparation
-
with independent quality monitoring of the finished sand line
Electric melting shop
-
2 MF melting furnaces with a capacity of 6 tonnes each
-
1 MF melting furnace with a capacity of 5 tonnes
Annealing shop
-
Two shuttle kilns for 8 tonnes of annealing material each
-
a 2-t annealing oven with automatic atmosphere control, measurement data acquisition and inert gas atmosphere (nitrogen)
Core making
-
Automatic core shooters for COLD-BOX process
-
Automatic core sand preparation